If you’ve been watching the blog for a while, you may recall that I have a relic-grade VG1-5 rifle – I found it at a gun show in Belgium and brought it back home in my suitcase. It is far beyond salvaging into any sort of functional firearm, but I thought it was too interesting of a piece not to buy.
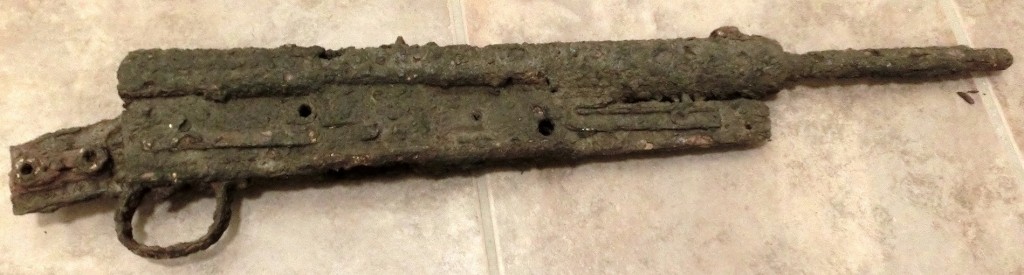
Well, I’ve been toying with the idea of using an electrolytic bath to remove the rust and see what it looks like underneath…but I’m not really sure if I should. There are some areas that are totally worn away, like the rear of the receiver and the trigger:
I’m not sure if an attempt at restoration would be wise. On the one hand, it would be really neat to get the rust off and see the original material – and that would prevent it from decaying further. However, it is a pretty cool artifact as-is, and I would hate to have it fall to pieces in an attempt to improve it. Of course, some of the metal is pretty thick (barrel, slide assembly, etc)…but other parts are really thin, like the sights.
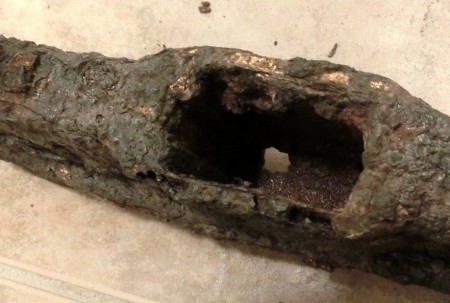
For those who aren’t familiar with it, an electrolytic bath is a simple ionized solution (water and baking soda) with a low voltage charge running through it. You immerse your rusty material to act as the cathode, and a piece of scrap ferrous metal to act as anode. The electrical charge causes material (rust) to dissolve off the cathode and adhere onto the anode. It’s the opposite of the process used to electrically plate objects. Here’s a practical example:
http://www.youtube.com/watch?v=_4NmM47XUPs
What do you folks think? Should I make an attempt at improving this thing’s condition at the risk of it coming out worse for some reason, or leave it as-is? I’d be especially curious to hear thoughts from anyone who has used the process before (I haven’t), but I would like to get everyone’s opinion:
[poll id=”4″]
I think the aim should be to stablise and conserver rather than restore..
The metal seems to be delaminating in places and perhaps the electrolytic process would further this process. Best to get some advice from a professional conservitor I think..
Also I think our little friend with the metal detector should be more careful in pulling up unidentified lumps of metal in what was a battlefield..! There is a lot more in the ground there in addition to scrap metal!
Totally agree with Bryden on all points. Stabilise and conserve what is left. I’m in the conservation business. Any restoration will most likely cause more destruction in this instance.
May we assume you’ve seen the following video series? http://www.youtube.com/watch?v=B28_VN8Q6YE It’s a pretty awesome demonstration of what one can do with some patience, electrolyte bath, and other tools of the trade. I recommend it.
Normal technique to remove this kind of oxide buildup on an iron or steel object is to sink the item in an agitated, hot, phosphoric bath with a surfactant package. The phosphoric acid rapidly reduces the metal oxides and, when the underlying iron is exposed to the bath, a protective iron phosphate layer is formed, stopping the acid reduction reaction. This iron phosphate layer is oleoscopic and a good basis for rust inhibitors or lacquer, the typical long term preservatives used by museums.
The electrolytic technique you mention actually works by dissolving (actually oxidizing) the elemental iron underneath the oxide layer, loosening the oxide layer. This removes a considerable amount of ‘good’ iron. The oxide layer is not electrically conductive, so it does not participate in the electrolytic reaction.
Oxide removal decision on archeological artifacts is usually made after X ray imaging to determine exactly how much ‘good’ metal remains. The density, and hence the radiopacity, of the oxide is half that of the underlying steel.
Might be tough for an individual to get a X-ray done on something like this, unless you are really friendly with your local doctor. Maybe you could take it in on Halloween if they still offer free x-rays of candy and treats.
Hi John,
You actually get quite the opposite effect with electrolysis, the atomic hydrogen released, reduces the oxide to iron metal, which can then be washed or brushed off as a loose black dust. there is no additional oxidation of the underlying metal, although it is left in a sufficeintly clean state that unless it is passivated immediately, it will flash rust.
Keith –
No. Hydrogen reduction of metal oxides only happens at much higher temperatures, above 500 C, and in the presence of halide ions like fluorine or chlorine. Metal oxides simply do not conduct enough electricity at temperatures below the boiling point of water to effect significant reduction. Electrolytic reduction of tenacious metal oxides is done in high temperature salt baths and is known as the Hall-Herault (alumina reduction) or Kroll (magnesia, zirconia reduction) processes. Iron oxides, in this case magnetite (Fe3O4), can be reduced carbothermically or with reducing acids, so electrolysis is not used in iron production processes.
The cleaning mechanism of the proposed aqueous electrolysis process is the conversion of good underlying metal to oxide, which has half the density (and hence twice the volume), of the underlying metal consumed. This volume creation produces high levels of compressive stress under the crud oxide which ‘pops’ it off. It is almost identical to the cleaning effect of a strong oxidizing acid, like hydrochloric acid – and almost as destructive to the underlying good metal.
Any good NDT operation inspecting welds should be able to make a quick shot on this piece. The Phoenix ASNT chapter should be able to line you up with someone who is capable. I can get you some contacts later today when I get some free time.
John,
In the electrolytic cleaning, the piece to be cleaned is the cathode in the circuit. conditions are reducing, hydrogen, not oxygen is being released, the cleaning effect is not due to further oxidation of the underlying metal, that oxidation is happening over at the anode, where if you are using a piece of scrap steel, the oxidation is pretty spectacular.
There is some adsorption of hydrogen occuring into the underlying metal, and also reduction of the oxide coating, the process is the same one as using a “hydrogen” electrode (hydrogen adsorbed onto the surface of a platinum electrode when demonstrating the electro negativity of a metal. In this case, Iron is less reactive than the hydrogen and is reduced. The same effect can also be achieved by reacting zinc or aluminium in a strong alkaline solution with the piece to be de rusted, in there with it, even without an electrical contact between the sacrificial metal and the piece to be cleaned, it is the release of atomic hydrogen which is doing the reduction.
The reason that electrolysis is not used for the commercial production of iron is simply that there are cheaper ways of doing the job on a production scale, for example blast furnace or direct reduction with natural gas to sponge iron.
a strong oxidizing acid, like hydrochloric acid
Of all the strong acids you had to pick the one that’s not oxidizing…
Chlorine ion valence is minus 1. When it compounds with iron it contributes its extra electron; definition of oxidation.
The only thing worth to put in an elektro lytic bath, are cannon barels recowerd from the sea. the current will destroy smaler items I hade some susses in boyling smaler iron items in oil(do it outside Ypur wife will skinn you if yo do it in the kitchen. I restored an MG 81 to working kondition thid way. a pease of the gunners finger, was still in the trigger guard. i found his name in the arcive he crashed in a moore in 1944 in Denmark
Please Ian!!!
This is now a piece of history. The restoration will set it to another level…..to that of absurdity.
I’m learning a lot about how to remove corrosion. Great stuff. But I’m with Dimitris. I won’t go as far as absurdity. Yet cleaning it up will remove the story that goes with it. If you had another similar piece or multiple pieces I’d say go ahead – try one. But only one?
You might call around to chiropractors in your area. One here (Arkansas) has an old film x-ray machine which are cheap because of the advent of digital machines.
I certainly wouldn’t try to clean it until I was sure there would be something left after cleaning.
From the appearance, I think soaking it in a mixture of paraffin and mineral spirits (paint thinner) would be the best course. That would prevent further deterioration and preserve what you have. I use it as a wood finish, but I think it would be a good choice for this situation. Be aware that the solubility of paraffin in mineral spirits is very temperature sensitive. You don’t want it to become super saturated because of a temperature change as that will produce a heavy coat of excess paraffin. A saturated solution made up at 80 F will be problematic at 60 F.
The idea is to deposit paraffin by evaporation. It will need to stay outside for a week or two if you decide to do this for the smell to dissipate.
Hi Ian,
I do use electrolytic cleaning on big heavy parts (bits of lathe and milling machine castings).
I would not use electolysis on that particular piece.
I suspect that a lot of the former sheet metal is either entirely rust, or else so thin and moth eaten, that it would not survive long if the rust were removed.
Steels tend to develop deep pits as they rust (in contrast to some cast, and indeed some wrought irons, on which the rust only forms a self limiting surface coating), whatever metal is left underneath the rust will show those deep pits when the rust is gone.
I don’t know the full process for rusty steel, but I think you’d be better off slowly and gently impregnating the rust with some form of high melting point, rust inhibiting wax or plastic to inhibit any further deterioration or breakdown of the rust.
On organic remains (not metal!) I’ve used PVA adhesive, watered down to the consistency of un skimmed milk, and left the part to impregnate with that for several weeks or months. It has prevented things like woolly mammoth teeth which I’ve found, from falling to pieces on exposure to air. It isn’t actually permenant, as eventually the acetate will be released as acetic acid, which will destroy the fossil, but it is the best temporary fix available to me.
There will be simillar combinations of wax or plastic in an organic solvent which can be used for rusty steel.
Keith –
“There will be simillar combinations of wax or plastic in an organic solvent which can be used for rusty steel.”
MIL-PRF-16173E Grade 2 Class 1 or MIL-C-83933A rust inhibitors are what you are looking for. Paraffin wax dissolved in xylene with barium sulphonate added as a rust inhibitor. Here is a commercial product which meets these requirements:
http://www.lpslabs.com/product-details/612
Thin it with xylene (a very safe and fireproof solvent) and use an ultrasonic bath to drive it into the crud oxide. More expensive and way slower than phosphoric acid treatment. Leaves some oxide behind.
These inhibitors are absolutely the best rust inhibitor for gun collectors. Leaves a rust inhibiting thin wax film which prevents corrosion for two years in outdoor exposure. Don’t use it on copper or copper alloys, though, because sulphonates tarnish them.
xylene (a very safe and fireproof solvent)and use an ultrasonic bath
Don’t try this at home, xylene is a highly flammable, with a flash point of 77F.
You can extinguish lit matches and cigarettes in xylene without any drama. It just doesn’t burn very well at all.
John,
I suspect that there is very little of the sheet metal left under the rust, I’d therefore be very cautious about using anything which would break that rust up.
An ultrasonic bath would be likely to break up the rust – fine on a heavy section piece, but with Ian’s VG, he’s quite likely to be left with a few deeply corroded heavy pieces, and a bucket full of rust fragments (which he might be able to pass off as a 1970s Alfa Romeo, in need of a little restoration).
It is Ian’s choice in the end, but if it were my piece, I’d be looking at ways to get that rust impregnated, probably with the products you suggest, but very gently, slow low heating (not over 100 C) and possibly using a vacuum pump, again, dropping the pressure very slowly, to draw water and air out of the rust and to encourage wax or plastic resin to penetrate.
I agree!!! Please, leave it the way it is now. I think that in the best case, even thick parts will not look much better enough after removing rust, and the thin parts will be ruined. It would be better to protect the piece someway to avoid it getting worse… and use it as a part of a set for a Nazi zombie comeback from his last ditch trench-grave!!! 😉 Putting jokes about exploiting the Zombie hype apart, I think it is really a valuable historical item as is. It will never show again as good as a new made and fully functional replica.
It is a relic and will never be more than a relic. The current condition is part of its history. Nothing you do will change that, and you risk destroying it just out of curiosity.
Is satisfying your curiosity worth it? Only you can make that decision. If it were mine I would enjoy it for what it is. There are plenty of nice VG1-5s out there. I doubt that there are very many relics like this in the US.
If you do get the rust off, you will have the firearms equivalent of ZsaZsa Gabor in a miniskirt.
Thanks!
The milk in my tea just curdled and turned to cheese
Before you do the VG1-5 rifle i would recommend trying something else first , the first time i try something i am way to likely to make stupid mistakes.
if you can have it x rayed or something like that , it may be that the thing is to far gone to do anything with it
Keith, that mental image was intentional, lol. I hope the Forgotten Weapons folks have the same reaction. Sorry for spoiling your tea!
Careful: there might be no more than a ‘rust-crust’ (dunno the word in english) left, with a hollow space where the metal used to be. What you should do is x-ray the thing first, see what the preservation of the metal components is and then fill up the hollow spaces with a sort of resin. Then the rust can be removed. You risk dissolving the entire thing otherwise. These guys do it all the time http://www.a-d-w.be/ndl/
Ian;
You might want to check this out before doing anything;
http://www.historicjamestowne.org/the_dig/dig_2013_01_29.php
These people know what they’re doing in this department, notably the do’s and (more importantly) the don’ts.
cheers
eon
Ian –
I am an ASNT member, but in the Michigan section. Our guys up here don’t do a lot of X ray work; most of this happens down in Texas/Oklahoma/Louisiana. Here is the contact information for the section leader of the Arizona section:
Contact: Dale Lynn
(480) 296-8611
E-Mail: dale.r.lynn@hotmail.com
Meeting Day: Third Thursday
Location: Coach & Willie’s – 412 South 3rd Street Phoenix, AZ 85004
Give him a call or drop into the section meeting. Engineers love this kind of project and I am certain someone there will assist you without shredding your wallet.
Thanks, John! I will definitely give them a call, and see what we can work out. Although given the number of areas where I know there isn’t any material left (because it’s completely rusted through) it sounds like I shouldn’t try to take the rust off regardless of how an x-ray examination turns out. It would still be really neat to see, though.
Ian try to mix molasses with water and place the piece in it for a couple of days. Thats what i do with car parts. after a day or two you can just wash the rust away and it wont eat the metal!
A few notes on the video.
I used to use an old fashioned battery charger as a power source, I find that the new ones with electronic control cut out with even moderately strong solutions. What I have found to be very effective though, are old laptop chargers. Given Ian’s background, I suspect he has a good source of DC power supplies.
I would need to look up the relative electro negativities of iron and magnesium to be certain, but I would suspect that the suggested two volts is a tad on the low side for cleaning lightweight alloy aircraft castings (the iron-magnesium cell made by the electrodes will have almost 2 volts working the opposite way to your power supply), If you’ve got light weight alloy parts, six volts or more would be a good idea, as would be having the power on before the part comes into contact with the bath, as alkali baths (especially if they are hot) really do fizz with aluminium magnesium and zinc.
The video suggests not using stainless steel as the anode. The reason for that is that oxidizing alkaline conditions, such as these, can potentially produce hexavalent chromium (Erin Brokovich…).
I checked out the reactions of hexavalent chromium at a previous job, and it turns out that even as week a reducing agent as ferrous sulphate (or iron or steel swarf) rusting in the solution for a few days is enough to reduce any hexavalent chromium to a lower oxidation state. Vitamin C does the job very nicely too. If you are in the US, it would still be best to keep quiet about any electrolysis with metals, as the EPA seems to get all excited about “electro-plating”.
Washing soda (sodium carbonate) seems to be as good an electrolyte as any. I started with using sodium hydroxide (Lye / caustic soda) and found it needlessly unpleasant, as the spray from the gas bubbles bursting is enough to sting any nearby skin, and contact with the spray mist even several feet away is very painful to eyes, nose and throat.
My strong and as professional restorer throw it to scrap..
Its not worth it because of very strong metal decomposition unless you want just mixed with epoxy or braze it just for decoration or museum view..
Rather than this it not worth it,it would never be able to become a living firearm again…
I been restore certain things before like Luger or P38 and believe to me its not an easy job,first it need to be cleaned completely from rust,corrosion,pitting,rusted sinks,etc than you need to sand it with abrossive materials or tungsten cutters..
After all surfaces cleaned area of work fully visible and revealed,spots that’s been disintegrated would recquires to dremel or grind em off and second factory blueprints recquires in order to see readings in millimeters mostly science I from Europe I only expertised on metrical readings,third important part you need to know how to use measuring tools and ecquipmant such as calipers and micrometers (dial indicators for machining aplications) because without those you wont be able to complete critical tasks,fourth very important part you need to be an ace welder that’s know how to use welding machines such as arc,mig and tig oprionaly spot welder than you be able to accomidate those tasks…
Sometimes it is very complicated for weld or reweld damaged areas,wrong temperature neather melt metal or make it turn or band for instances,another common problem different steel or alloy material…
For example if you got a damaged bolt carriers or bolts repair procedure would normaly take 3 times weld and grind until metal would succesfuly sustained and upplied on repaired part..
As second task tuning and shaping deffenately table grinder,angle grinder,wiz wheel and dremel as finishing…
Always use measuring tools and blueprints to check factory readings othervise your repair would be worthless..
I was repairing certain parts and later turned out certain chippings appeared after grinding,certain welding repairs didn’t succeded than begin to regrinding it again and rewelding over until finaly everything matched readings…
While some maintainers not aware be ready to sacrifice certain areas of metal in order to fabricate new area and weld it in also commonly appeared problem…
In order to do professional restorations you need to love your job,thinking that you writing a poem or drawing a picture it really must be perfect othervise you wont be able to accomplish your restorations…
Sometimes I feel boared and stressed out and if I in the move like this I usually never get lucky…
Well,
If you want to skip spanding money on certain minor parts you need to learn how to fabricate your own ones,it helped me a lot to save at least 400 bucks for over spanding…
For example if you want to save certain 35 bucks,56 or 85 by buying Luger barrel extension locking lever try build your owmn by estimating metal types,quality and factory readings simple as that..
On normal scales it takes 2 o 3 parts,an cylindrical rod which have to be strict 7mm than middle of it have to be weld professionaly and thickness totally with welded finished area need to be 9,5mm no more and no less if more it wont fit in frame hole small wont hold barrel extension secured and final critical part is side bar which carefuly have to be weld with cylindrical rod to forming one main lever,there have to be a groove which will hold side plate with trigger lever..
if groove not done correctly and too small side plate wont be secured and will come out and if more longer than factory readings wont be able to lock…
Sometimes believe me or not smaller parts motre complexed than larger parts and repair taking on watch repairing skills to finish all operations..
My major advises if you donot possest knowledge about measuring tools or ecquipmant plus welding knowledge while other peoples not even know what rotory tools is like dremel donot even attempt to do any repairs or restorations because A you be injured during or after your unsuccessful meintanance B you might injure others if somebody decided to buy your repaired master piece…
If you do something do something to yourself if it woth it all time and your energy to accomplish certain repairings..
Very important warnings:
Donot attempt to merge metal with non ferrous materials like Epoxy or brazing this would injure you and if you decide to reactivate certain things would probably kill’s you..
Rule number 1 epoxy wont be hold on steel or steel alloys and if under certain conditions temperature get cold or hot epoxy disintegrates from metal surface..
Brazing process is cheap and ergonomical to safe certain money on expansive stainless steel parts,trick is easy first sand or grind repaired area if it not major than upply brazing after use finest sand paper,clean the whole part with non ionized solution and dry it…
If you know how upply chrome coating but donot mistake with cheap aluminum painting..
Chrome coating greatly prevents rust to get on metal surfaces,this my personal theories and if you got a gas pistons and want restore them use that option it will save you lots of money..
No matter how rare certain things or items is first ask yourselves is it woth it??
Second check if this an repairable part or item,if no than donot buy to waste your moneys…
There is usualy 4 grades of damages that parts or items have :
1st surface rust,this is most easy and not hard problem to restore items but be aware that’s items like that will cost as normal items because no physical damages on it,in that condition use fine coasted sand paper than after everything clean try to blue it or oxidation process to prevent this part or model to get ever rusty again,in some cases I see certain restorers would also use special enamel paint over it so firearm or part wont be ever get chance to get rusty again…
2nd damage is metal pittings:
This depands at which grade those pittings is and how deep they are,if shallow to moderate grade it recquires that’s you grind area and reweld it slightly,sheetmetall I would strongly advise tig welder science it operate on Direct Current and ampage jump is absent so items not get melt or desitegrated but accurately repaired,after welding it need to be dremeled and sanded the rest of finishing similar to 1st category…
3d damage point that’s metal is chiiping away at some points or deeper rusted sinks which sometimes laying hidden under pitted areas,certain cases it recquires to deplete or remove damaged area or aperture in order to save actualy rare relic which for instance not necessary firearm,it might be a classic car,truck repair or something similar for examples arches in building if they cost certain value..
Damaged areas getting removed and new similar fabricated surfaces or apartures get build than it get upplied in damaged areas and weld than professionaly restored…
In some rare cases certain good parts for example front,middle or end getting saved while everything else get removed and refabricated than fused together again,believe it or not its like to be a surgeon,architect and mechanic at ones in order to complete those difficult tasks,its like puzzles or mazes to solve..
4th grade of damage is metal disintegrated,metall breaking and chipping apart like for that same photo of what we got voted on..
In this case firearm unrepairable and makes no absolutely any historical values…
In Europe items like this cost coins and absolutely make no attraction,for those who don’t posest any skills of craftsmanship may buy anything even something stupid for 1000 bucks than years later throw it on junk which is very common in USA..
I’ve used this process several times for motorcycle engine parts. I wouldn’t do it with the VG-1 you have. IMO, I don’t think you’d have much left.
All this talk of X-ray and nobody recalls that we have a member who runs an X-ray department?
Ian, for you I would be willing to take any type of radiograph possible on any subject, within the system limitations. Although I do not specifically run a metallurgic radiography unit, I do have a digital system which can take an unlimited amount of pictures at a variety of exposure factors. Might not be of the same quality as a dedicated metallurgic unit, but it would only cost you shipping, and I could take any number of images from any angle you’d like. If this is something that would be useful to you at any point please e-mail me and we can discuss the specifics and the limitations.